The automobile and the assembly line are two of the most transformative inventions of the 20th century, and Henry Ford is the visionary who united them. In 1913, Ford introduced the moving assembly line to mass-produce his Model T automobile, revolutionizing manufacturing and fundamentally reshaping society. This groundbreaking innovation made cars affordable for the average person, spurred economic growth, and set the stage for the modern automotive industry.
Henry Ford: A Visionary Industrialist
Henry Ford was born on July 30, 1863, in Greenfield Township, Michigan. He displayed an early interest in mechanics, often dismantling and reassembling machines on his family farm. After working as a machinist and engineer, Ford turned his attention to creating a reliable and affordable automobile for everyday use.
By 1903, he founded the Ford Motor Company and, five years later, introduced the Model T. Known as the “Tin Lizzie,” the Model T was praised for its durability, simplicity, and affordability. Ford’s mission was clear: to make the automobile a practical necessity rather than a luxury for the wealthy.
The Birth of the Assembly Line
Before Ford’s innovation, manufacturing processes were slow, labor-intensive, and expensive. Skilled workers assembled products from start to finish, resulting in high costs and limited production. Ford recognized that a more efficient method was needed to meet the growing demand for his Model T.
Ford and his team studied existing manufacturing techniques, including those used in meatpacking plants and other industries. Drawing inspiration from these practices, they developed the moving assembly line, a system where vehicles were assembled in stages as they moved along a conveyor belt.
The assembly line was first implemented at Ford’s Highland Park plant in Michigan in 1913. This innovation revolutionized manufacturing by:
- Dividing labor into smaller, specialized tasks.
- Reducing the time required to build a Model T from 12 hours to just 90 minutes.
- Allowing workers to remain stationary while the car parts moved to them.
How the Assembly Line Worked
The assembly line was designed to streamline production by breaking the process into sequential steps. Each worker focused on a specific task, such as attaching wheels or installing the engine. The line moved at a consistent pace, ensuring efficiency and uniformity.
Key elements of Ford’s assembly line included:
- Interchangeable Parts: Standardized parts made it easier to assemble cars quickly and accurately.
- Conveyor Belts: Mechanized belts transported parts and vehicles along the production line.
- Specialized Labor: Workers were trained for specific tasks, reducing the need for highly skilled labor.
This system not only increased production speed but also lowered costs, making the Model T affordable for the average American.
Impact on the Automotive Industry
Ford’s assembly line had a profound impact on the automotive industry, transforming it into a mass-production powerhouse. By 1924, Ford was producing nearly 2 million Model Ts annually, and the price of the car had dropped to $260—about $4,000 in today’s dollars. This affordability made car ownership accessible to middle-class families, revolutionizing transportation.
Other automakers quickly adopted Ford’s methods, leading to fierce competition and rapid innovation. The assembly line became the standard for manufacturing not only cars but also a wide range of goods, from appliances to airplanes.
Social and Economic Effects
Ford’s assembly line was more than a manufacturing innovation; it was a catalyst for profound social and economic change.
A. Economic Growth
The efficiency of the assembly line reduced production costs and increased profits. Ford’s decision to pay his workers $5 per day—double the prevailing wage—attracted skilled labor and boosted employee morale. This wage policy, introduced in 1914, also created a new class of consumers who could afford the very cars they built, driving economic growth.
B. Urbanization
The rise of affordable automobiles encouraged urban expansion and suburban development. People could now commute to work from greater distances, reshaping cities and transportation networks.
C. Cultural Transformation
The automobile became a symbol of freedom and individuality. It gave people greater mobility, enabling them to travel for leisure and explore new opportunities.
Challenges and Criticism
Despite its success, the assembly line faced criticism and challenges:
- Monotony for Workers: The repetitive nature of assembly line tasks led to worker dissatisfaction and high turnover rates. Many found the work physically and mentally exhausting.
- Resistance to Change: Some industries were slow to adopt the assembly line, fearing it would devalue skilled labor or disrupt traditional practices.
- Environmental Impact: The mass production of automobiles contributed to urban sprawl, air pollution, and reliance on fossil fuels.
Ford addressed some of these issues by improving working conditions and introducing leisure facilities at his plants. However, the environmental consequences of the automobile industry remain a significant concern today.
Ford’s Legacy and the Evolution of Manufacturing
Henry Ford’s assembly line fundamentally changed how goods are produced. His methods have been adapted and refined over the years, leading to innovations such as:
- Lean Manufacturing: Developed by Toyota, this approach minimizes waste and maximizes efficiency.
- Automation: Robots and advanced machinery now perform many tasks on modern assembly lines, increasing precision and reducing costs.
- Customization: Advances in technology allow manufacturers to produce customized products without sacrificing efficiency.
Today, Ford’s legacy lives on in factories around the world, where his principles of mass production continue to drive innovation.
The Broader Impact of Ford’s Invention
The automobile assembly line influenced industries far beyond manufacturing. Its principles have been applied to healthcare, food production, and even software development. The idea of breaking complex processes into smaller, manageable steps has become a universal strategy for achieving efficiency and scalability.
Ford’s assembly line also laid the groundwork for globalization. By making products affordable and accessible, it created new markets and opportunities for international trade. The automobile, in particular, became a global phenomenon, transforming cultures and economies worldwide.
Henry Ford’s introduction of the assembly line in 1913 was a turning point in history. It revolutionized manufacturing, democratized automobile ownership, and reshaped society in countless ways. Ford’s vision of making cars affordable for everyone not only changed how people traveled but also how they lived, worked, and connected.
The assembly line remains one of the most significant innovations of the modern era, influencing industries and economies across the globe. Henry Ford’s legacy is a testament to the power of innovation and the enduring impact of transformative ideas.
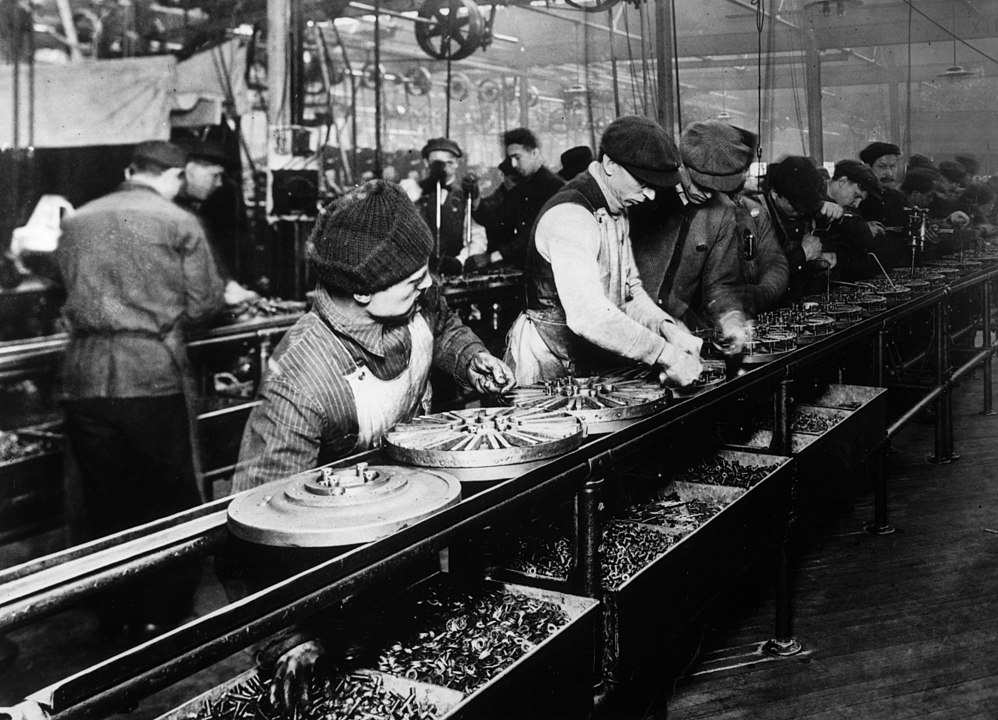
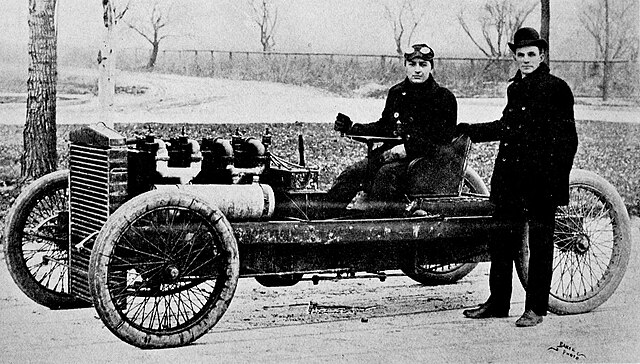
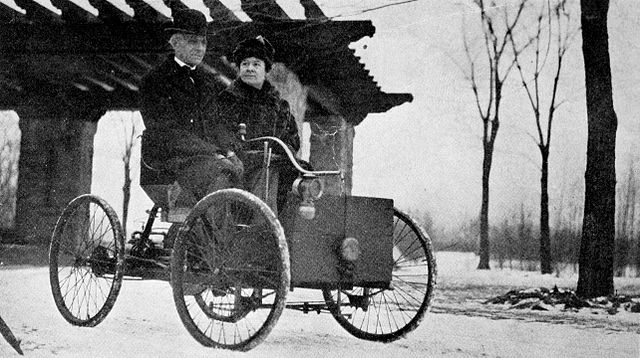